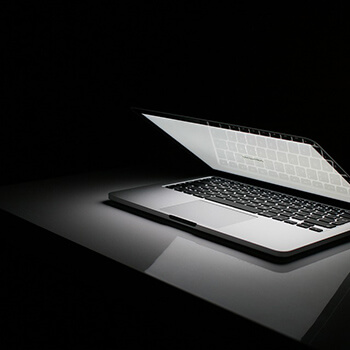
Some systems disable alternator
Some systems disable alternator field (rotor) power during wide open throttle conditions. Disabling the field reduces alternator pulley mechanical loading to nearly zero, maximizing crankshaft power. In this case the battery supplies all primary electrical power.
Gasoline engines take in a mixture of air and gasoline and compress it by the movement of the piston from bottom dead center to top dead center when the fuel is at maximum compression. The reduction in the size of the swept area of the cylinder and taking into account the volume of the combustion chamber is described by a ratio. Early engines had compression ratios of 6 to 1. As compression ratios were increased the efficiency of the engine increased as well.
With early induction and ignition systems the compression ratios had to be kept low. With advances in fuel technology and combustion management high performance engines can run reliably at 12:1 ratio. With low octane fuel a problem would occur as the compression ratio increased as the fuel was igniting due to the rise in temperature that resulted. Charles Kettering developed a lead additive which allowed higher compression ratios.
The fuel mixture is ignited at difference progressions of the piston in the cylinder. At low rpm the spark is timed to occur close to the piston achieving top dead center. In order to produce more power, as rpm rises the spark is advanced sooner during piston movement. The spark occurs while the fuel is still being compressed progressively more as rpm rises.18
Źródło: https://en.wikipedia.org/wiki/Internal_combustion_engine
History of electric motor
Perhaps the first electric motors were simple electrostatic devices created by the Scottish monk Andrew Gordon in the 1740s.2 The theoretical principle behind production of mechanical force by the interactions of an electric current and a magnetic field, Amp?re's force law, was discovered later by André-Marie Amp?re in 1820. The conversion of electrical energy into mechanical energy by electromagnetic means was demonstrated by the British scientist Michael Faraday in 1821. A free-hanging wire was dipped into a pool of mercury, on which a permanent magnet (PM) was placed. When a current was passed through the wire, the wire rotated around the magnet, showing that the current gave rise to a close circular magnetic field around the wire.3 This motor is often demonstrated in physics experiments, brine substituting for toxic mercury. Though Barlow's wheel was an early refinement to this Faraday demonstration, these and similar homopolar motors were to remain unsuited to practical application until late in the century.
Jedlik's "electromagnetic self-rotor", 1827 (Museum of Applied Arts, Budapest). The historic motor still works perfectly today.4
In 1827, Hungarian physicist Ányos Jedlik started experimenting with electromagnetic coils. After Jedlik solved the technical problems of the continuous rotation with the invention of the commutator, he called his early devices "electromagnetic self-rotors". Although they were used only for instructional purposes, in 1828 Jedlik demonstrated the first device to contain the three main components of practical DC motors: the stator, rotor and commutator. The device employed no permanent magnets, as the magnetic fields of both the stationary and revolving components were produced solely by the currents flowing through their windings
Źródło: https://en.wikipedia.org/wiki/Electric_motor
Car - mass production
The large-scale, production-line manufacturing of affordable cars was debuted by Ransom Olds in 1901 at his Oldsmobile factory located in Lansing, Michigan and based upon stationary assembly line techniques pioneered by Marc Isambard Brunel at the Portsmouth Block Mills, England, in 1802. The assembly line style of mass production and interchangeable parts had been pioneered in the U.S. by Thomas Blanchard in 1821, at the Springfield Armory in Springfield, Massachusetts.33 This concept was greatly expanded by Henry Ford, beginning in 1913 with the world's first moving assembly line for cars at the Highland Park Ford Plant.
As a result, Ford's cars came off the line in fifteen-minute intervals, much faster than previous methods, increasing productivity eightfold, while using less manpower (from 12.5-man-hours to 1 hour 33 minutes).34 It was so successful, paint became a bottleneck. Only Japan Black would dry fast enough, forcing the company to drop the variety of colors available before 1913, until fast-drying Duco lacquer was developed in 1926. This is the source of Ford's apocryphal remark, "any color as long as it's black".34 In 1914, an assembly line worker could buy a Model T with four months' pay.34
Ford's complex safety procedures?especially assigning each worker to a specific location instead of allowing them to roam about?dramatically reduced the rate of injury. The combination of high wages and high efficiency is called "Fordism," and was copied by most major industries. The efficiency gains from the assembly line also coincided with the economic rise of the United States. The assembly line forced workers to work at a certain pace with very repetitive motions which led to more output per worker while other countries were using less productive methods.
Źródło: https://en.wikipedia.org/wiki/Car#Mass_production